立井提升系统的智能化升级,是以副井提升机房作为集控中心,不仅配置了主井提升机远程操作台、显示终端及声光报警装置,还实现了副井司机远程操控与主井无人值守的一体化运行,彻底取消了主井岗位司机,大大提升了作业效率和安全性。
远程视频监控:副井集控室新增多处监视屏,对提升机、变压器、操作台、平衡尾绳以及井口井底等重要区域实施全天候实时视频监控,确保及时掌控现场运行情况。
智能巡检系统:利用轨道式巡检机器人和定点监测系统取代传统的人工巡检。机器人依托高清摄像技术和红外热成像技术,可准确捕捉设备温度异常,实时上传至平台并触发告警。此外,巡检机器人还能自主完成对高低压室、传动室等核心设施的多重监控,检测结果直观呈现于管理平台,支持远程在线监测与现场处置相结合。
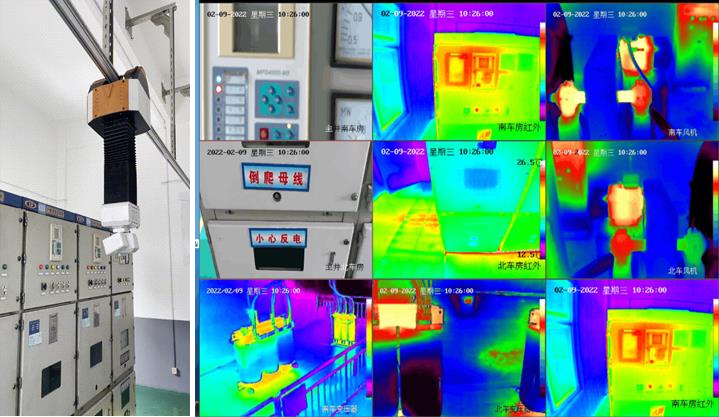
井筒智能监测系统:引进胶轮自主发电和井筒无线传输技术,打造了一套先进的井筒巡检系统,对井筒内的滚轮罐耳、罐道、罐道梁等关键装备进行视频检测,同时实时监测钢丝绳张力和箕斗载重,确保提升过程的安全可控。此系统具备强大的数据采集、存储和分析功能,可生成设备状态分析报告,及时提出故障处置建议。
设备状态监测:在提升机房及提升机关键部件如主电机、轴承等位置安装58组监测传感器,对转速、振动、温度、湿度、烟雾、噪声等多种参数进行全面监测与预警,有效预防突发故障。设备健康管理系统借助物联网传感器和智能机器学习算法,对设备运行数据进行深度挖掘,提前预判潜在故障,从而优化设备运行状态,显著降低故障率(由0.5%降至0.2%),延长设备使用寿命。
得益于上述智能化建设,唐口煤矿成功实现主井无人值守自动化运行,大幅减少了人力成本,每日减少了原本需进行的22次人工巡检,共节约了12个岗位人员,极大减轻了工人的劳动强度,同时也提高了工作效率。井筒智能监测系统与设备状态监测系统的无缝对接,有力保障了提升系统的安全稳定运行,有效避免了过度维护和非必要停机